عیوب و ناپیوستگی های شایع در اتصالات جوش
مقدمه
در حالیکه یکی از اهداف در عملیات جوشکاری کاهش هزینه تمام شده یک اتصال است، اما همزمان و در کنار آن تلاش برای تولید جوش سالم و بدون عیب و نقص مورد توجه میباشد. تا بحال تعداد زیادی کشتی، پل، مخزن و اسکلت های فلزی در اثر ایجاد برخی عیوب در فلز جوش یا منطقه مجاور آن شکسته شده و موجب خسارات مالی و جانی فراوانی گشته اند. معایب و مشکلات جوشکاری ممکن است در مراحل حرارت دادن و ذوب، رسوب دادن فلز جوش، انجماد و سرد شدن و یا در ضمن سرویس قطعه کار ایجاد و مشاهده شود.جوش ایده آل تقریباً غیر ممکن است و معمولاً جوش ها دارای معایبی می باشند که در این مقاله به شرح آنها می پردازیم.
پرشدن ناقصUNDERFILL
پر شدن ناقص زمانی رخ میدهد که فلز پر کننده به اندازه کافی برای پر کردن اتصال جوش در دسترس نباشد. پر شدن ناقص هم در سطح رویی و هم در ریشه جوش ظاهر میشود. دلیل اولیه پر شدن ناقص، تکنیک غلط جوشکاری است، مثلاً سرعت زیاد جوشکاری اجازه پر شدن اتصال و هم سطح شدن آن با فلز پایه را نمیدهد.
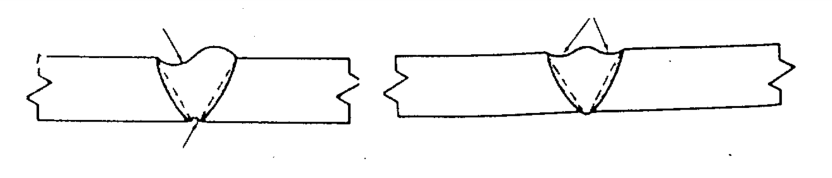
سر رفتنOVER LAP
نوع دیگر ناپیوستگی سطحی که از تکنیک نامناسب جوشکاری ناشی میشود، سر رفتن است. سر ریز شدن فلز جوش دورتر از کناره جوش یا ریشه جوش را سر رفتن می نامند. دراین نا پیوستگی فلز جوش روی فلز پایه مجاور سر میرود. این عیب عموماً به علت تکنیک نامناسب جوشکاری است. یعنی اگر سرعت جوشکاری خیلی آرام باشد، مقدار فلز پرکننده برای پر کردن اتصال زیاده از حد مورد نیاز خواهد بود و در نتیجه سر رفتن را خواهیم داشت.
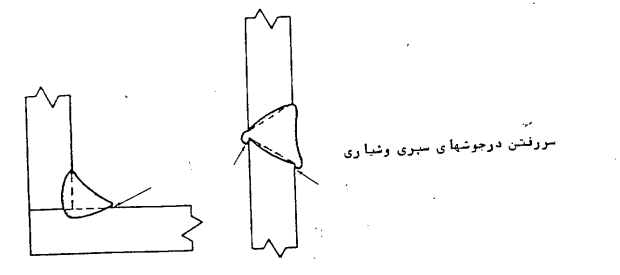
تحدب بیش از حدEXCESS CONVEXITY
این ناپیوستگی خاص تنها مختص جوش های سپری میباشد. تحدب عبارتست از حداکثر فاصله از رویه یک جوش سپری محدب تا خط واصل بین کناره های جوش. در محدوده ی معینی تحدب مخرب نیست و حتی از نقطه نظر استحکام مقداری تحدب در جوش سپری لازم است ولی اگر از حدی بیشتر باشد به عنوان عیب تلقی میشود. این مطلب هم از نقطه نظر اقتصادی( مصرف فلز پرکننده بیشتر) و هم از نظر حضور مناطق تیز اطراف جوش به خصوص در بارگذاری خستگی مطرح میشود. دلیل ایجاد تحدب آرام بودن سرعت جوشکاری یا تکنیک ناصحیح جوشکاری است.
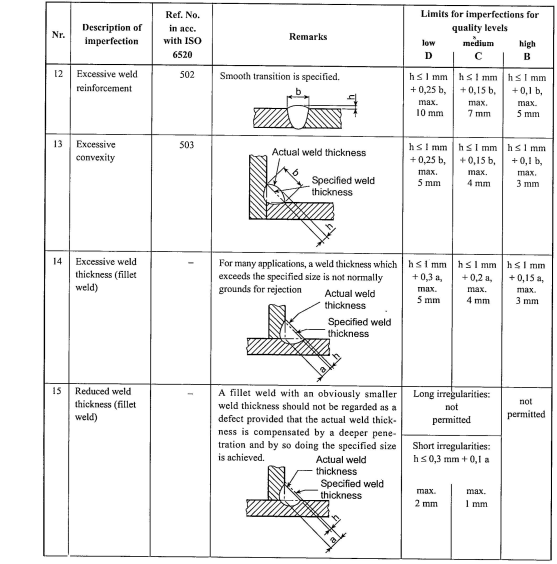
لکه قوسARC STRIKE
حضور لکه قوس ناپیوستگی بسیار خطرناکی را ایجاد میکند. لکه های قوس در نتیجه شروع قوس عمداً یا تصادفی روی فلز پایه دور از اتصال به وجود می آید. در اثر این رخداد، منطقه ای متمرکز شده از سطح فلز پایه، ذوب شده و سریعاً سرد می شود. لکه های قوس اصولاً توسط تکنیک جوشکاری غلط ایجاد می شوند. جوشکاران باید حتماً از خطرات لکه قوس آگاه باشند. راه حل این مشکل آغاز کردن قوس الکتریکی در خارج از قطعه مورد نظر است. از طرف دیگر اتصال نامناسب زمین به قطعه کار نیز سبب ایجاد لکه قوس می شود.
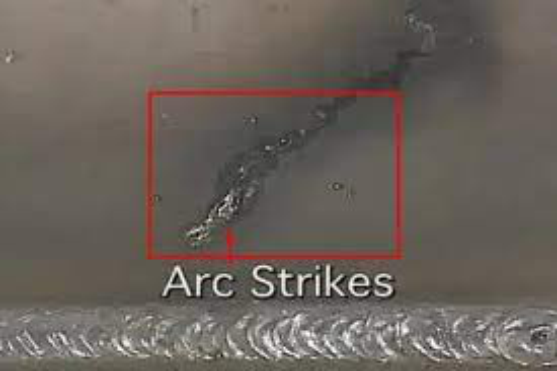
پاشش(ترشح) SPATTER
ذرات فلزی پراکنده شده در خلال جوشکاری که در تشکیل جوش نقشی ندارند پاشش معرفی میشوند. در این بخش عموماً ذراتی که در مجاورت جوش هستند مد نظر قرار گرفته شده ولی ذرات دورتر را نیز به عنوان پاشش در نظر می گیریم. دلیل ایجاد پاشش را می توان جریان بالای جوش دانست. بعضی از روش های جوشکاری طبیعتاً ترشح بیشتری نسبت به دیگر فرآیندها دارا هستند. به عنوان مثال استفاده از آرگون پاشش را به مقدار قابل ملاحظه ای نسبت به CO2 در جوشکاری کاهش میدهد.
تورق(جدالایگی) LAMINATION
این ناپیوستگی مربوط به فلز پایه است. تورق در اثر حضور آخال های غیرفلزی موجود در زمان تولید فولاد ایجاد می شود. این آخال ها به طور طبیعی اکسیدی هستند که در زمانی که فولاد هنوز مذاب است، تشکیل میشوند. در خلال عملیات بعدی نورد این آخال ها کشیده شده و تشکیل stringer را می دهند. اگر این stringer ها بزرگ باشند، آنها را تورق می نامند. گرمای ناشی از جوشکاری برای ذوب مجدد stringer ها در مجاورت جوش کافی است. لذا انتهای آنها می تواند ذوب شده و یا ممکن است باز شوند.
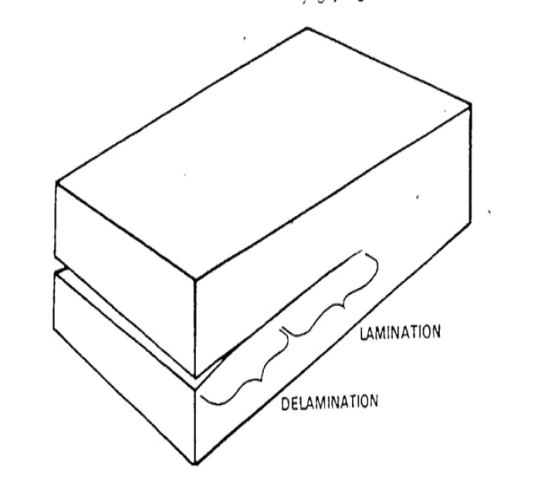
تخلخل و مکPOROSITY
تخلخل سوراخ یا حفره ای است که به صورت داخلی یا خارجی در جوش دیده میشود. تخلخل همچنین به صورت مک لوله ای، مک سطحی و سوراخهای کرمی نیز دیده میشود. خلل و فرج در جوش چندین نوع بوده که به قرار زیر است:
1-خلل و فرجی که در چند سانتی متری اولیه شروع جوشکاری در هنگام استفاده بعضی از الکترودها مشاهده میشود. این عیب در اثر فقدان اکسیژن زدایی کافی در ابتدای جوش است.برای پرهیز از این نوع خلل تدابیر مختلفی پیش بینی شده:
- شروع عملیات جوشکاری بر روی قراضه فولادی که قبلاً در ابتدای مسیر عملیات جوش الصاق شده است انجام میشود و پس از خاتمه جوش از قطعه کار جدا می شود.
-تکنیک یک گام عقب : نقطه شروع کمی عقب تر از محل شروع واقعی است. پس از آغاز جوشکاری، الکترود به ابتدای مسیر اتصال هدایت شده و عملیات جوشکاری ادامه می یابد. بدین ترتیب اگر خلل و فرج نیز ایجاد شده باشد با برگشت قوس و ذوب مجدد آن به احتمال زیاد برطرف می شود.
2- خلل و فرج در دامنه انجماد: این نوع حفره های ممکن است در سراسر جوش مشاهده شوند و خود دارای دو نوع شکل هستند که عبارتست از: 1) خلل و فرج های کروی شکل که به صورت متمرکز یا پراکنده در زیر جوش یا حتی روی جوش دیده می شوند. 2) نوع دیگر که به سوراخ های کرمی شکل یا مک هوا موسوم است. بعضی گازها در مذاب دارای حلالیت بوده که در درجه حرارت های بالا مقدار این حلالیت نیز افزایش می یابد. البته می توان پیش بینی کرد که در سطح انجماد گازها به حالت اشباع در آمده و مقدار اضافی از این حد به صورت حبابهایی در روی دانه های جامد جوانه زده و رشد میکنند. و در مواردی که شرایط مناسب نباشد حباب ها به حالت شناور یا در حین تکامل در لابلای دانه های جامد در حال رشد، حبس شده و به صورت خلل و فرج و یا سوراخ های کرمی شکل در فلز جوش باقی می مانند. بنابراین تنها راه جلوگیری از ورود گازها حذف عوامل ایجاد گازها نظیر رطوبت و چربی است. به عنوان مثال با پیش گرم کردن الکترود میتوان میزان هیدروژن ورودی را کاهش داد.
علل به وجود آورنده تخلخل یا مک به صورت موردی:
1-سطح فلز پایه آلوده باشد. مثلاً آلودگی های روغن، غبار، لکه یا زنگ.
2-الکترود نامناسب برای فلز پایه، مثلاً استفاده از الکترود روکش شکسته یا استفاده از الکترود مرطوب.
3-عدم محافظت گازی مناسب از جوش.
4-استفاده از فلزات پایه با مقادیر بالای گوکرد و فسفر.
5-زمان ناکافی برای فعل و انفعالات متالوژیکی در حوضچه جوش.
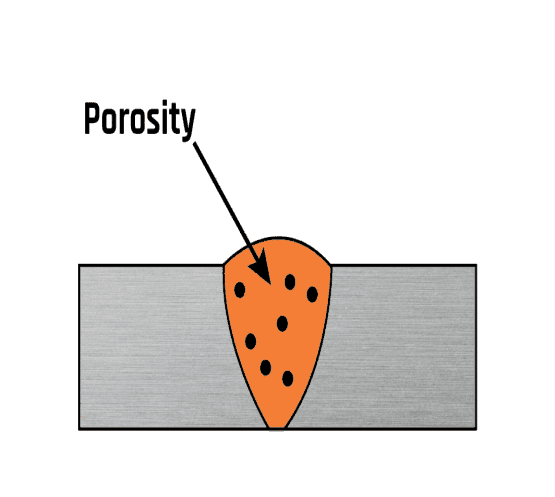
سوختگی و یا بریدگی کناره جوش UNDER CUTTING
سوختگی کناره جوش یا به عبارت دیگر وجود زبانه یا شکاف در اطراف منطقه جوش که به صورت منقطع یا پیوسته با عمق کم یا زیاد در سرتاسر مسیر جوش است را سوختگی می نامند. یا به عبارت دیگر شیاری که در کنار یا ریشه جوش که بر سطح جوش و یا فلز جوشی که قبلاً راسب شده است را سوختگی یا بریدگی کناره جوش می نامند.
عوامل بوجود آورنده بریدگی کناره جوش یا سوختگی:
1-استفاده از آمپر بالا
2-بالا بودن طول قوس
3-استفاده از الکترود با قطر کم.
4-سرعت بسیار زیاد حرکت جوشکاری.
5-حرکت موجی زیاد الکترود.
6-متمایل بودن زاویه الکترود به سطح اتصال.
7-بالا بودن ویسکوزیته و سرباره جهت ایجاد نیروی قوس نا درست
8-برای جلوگیری از این عیب باید از حرکت زیگزاگی مناسب، با مکث های کوتاه در کناره های لبه اتصال انجام داده و سرعت پیشرفت جوشکاری را کمی کاهش دهیم.
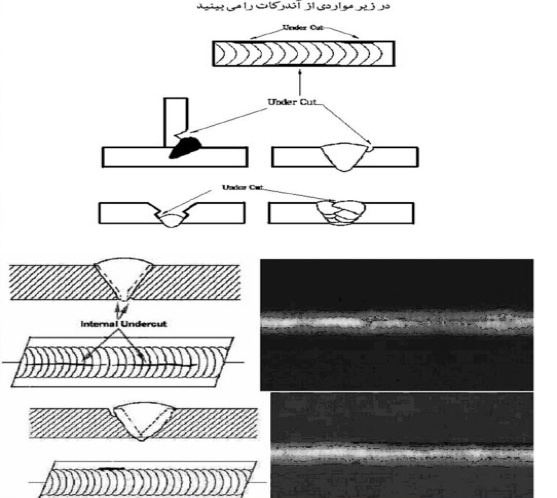
همراستا نبودن اتصالJOIN MISALIGMENT
از عیوبی که در اثر سوار کردن و مونتاژ غلط اجزا مورد جوش در کنار یکدیگر بوجود می آید، که معمول ترین آنها هم محور نبودن و همراستا نبودن دو سطح قطعه کار است. این عیب در بعضی موارد با پرس کاری برطرف میشود اما در بشتر موارد باید جوش را بریده و دوباره عملیات جوشکاری را با دقت تکرار کرد. این عیب ناشی از تکنیک عملیاتی نا مناسب می باشد که ممکن است استحکام جوش را تحت بعضی از تنش ها محدود کند.
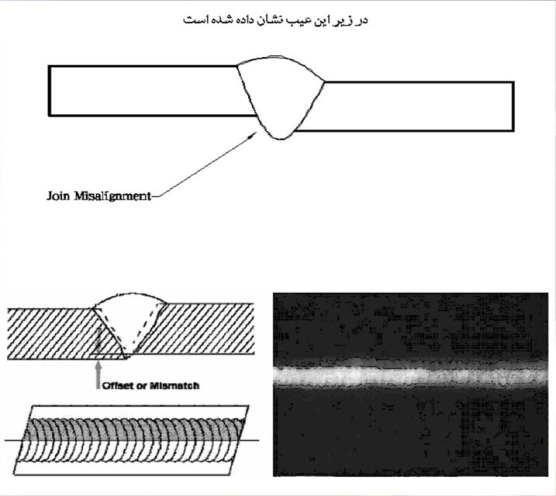
ترکیدگی یا ترکCRACKING
یکی از مهمترین، حساس ترین و مضرترین عیب در جوش ها ترک می باشد. ترک ناپیوستگی های صفحه ای است که بر اثر پاره شدن فلز جوش و فلز پایه ایجاد می شود. ترک فلز جوش می تواند در شرایط پلاستیک(ترک گرم) پدید آید و هم میتواند توسط شکست هنگامی که فلز سرد شده است(ترک سرد) بوجود آید. ترکیب شیمیایی، مواد مصرفی پارامترهای جوشکاری، طراحی قطعه و محل اتصال و شرایط عملی و تکنیکی در جوشکاری میتواند سبب تشدید یا تقلیل نوع خاصی از ترک شود. یکی از عوارض مهم ترک شکسته شدن قطعه بدون تغییر فرم پلاستیکی است که شکست ترد نامیده می شود. این نوع شکست در ابتدا بسیار کند بوده ولی پیشرفت بسیار سریعی دارد و ترک بوجود آمده در زمان کوتاه بدون نیاز به تنش ادامه یافته و شکست به وقوع می پیوندد.
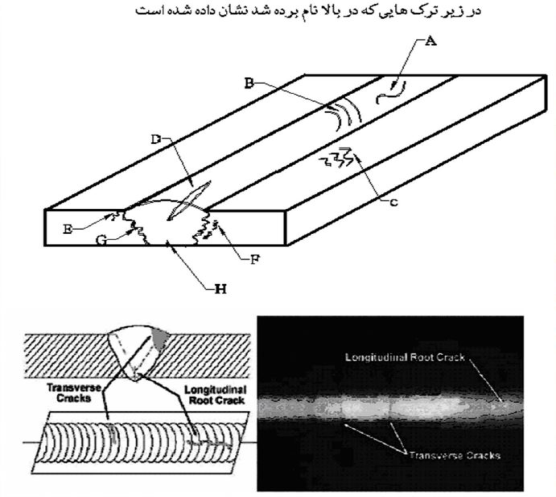